Solving the Woes of Cracking and Fraying in Vibration Knife and Cutting Machine Felt Belts
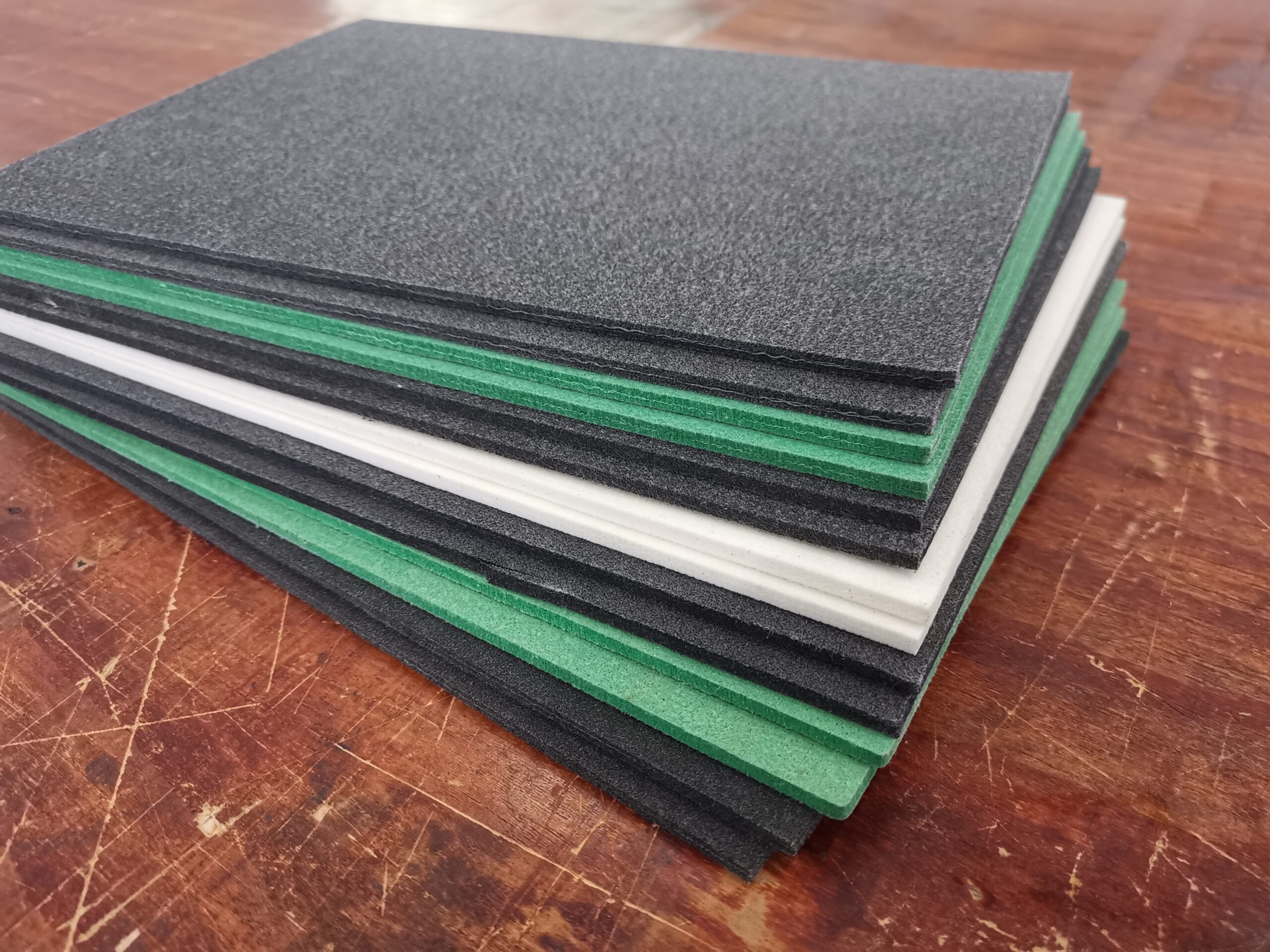
Introduction
In the operation of vibration knife and cutting machine equipment, the problem of felt belts cracking and fraying is quite common. These issues not only affect the performance of the equipment but also potentially lead to production delays and increased costs. In this blog post, we will explore the causes behind these problems and propose effective solutions.
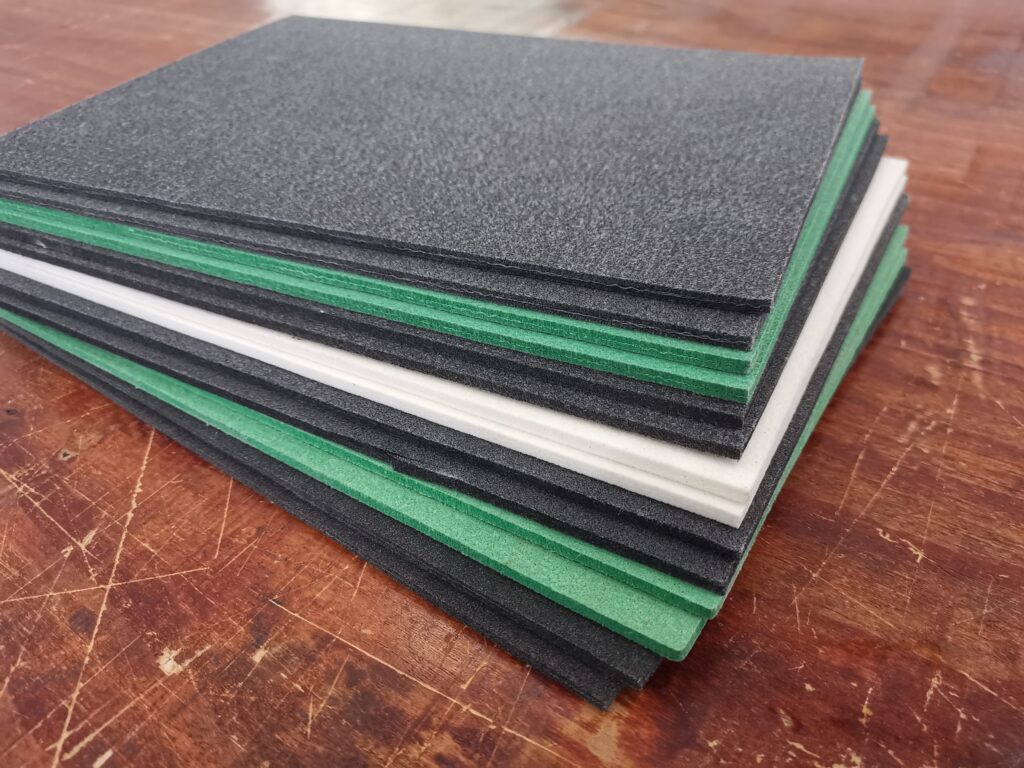
Causes of Cracking and Fraying
- Material Fatigue
Over time, the continuous stress and strain on the felt belt during the cutting process can cause material fatigue. Repeated bending, stretching, and contact with cutting tools and workpieces gradually weaken the internal structure of the felt belt, making it prone to cracking. - Incorrect Tension
Improper tension adjustment is another major culprit. If the felt belt is too tightly tensioned, it will bear excessive stress, accelerating the appearance of cracks. On the other hand, if the tension is too loose, the belt may slip, resulting in uneven wear and fraying along the edges. - Tool – Belt Interaction
The design and condition of the cutting tools can also impact the felt belt. Dull or misaligned cutting tools can cause uneven pressure on the felt belt, leading to localized wear and eventual fraying. Moreover, the friction between the tool and the belt during high – speed operation generates heat, which can degrade the material properties of the felt belt and cause cracking. - Environmental Factors
The working environment plays a role as well. High humidity can cause the felt belt to absorb moisture, changing its physical properties and making it more brittle. Extreme temperatures, either too high or too low, can also affect the flexibility and durability of the felt belt, increasing the likelihood of cracking.
Solutions
- Regular Inspection and Replacement
Establish a regular inspection schedule for the felt belt. Check for any signs of early wear, such as small cracks or slight fraying. Once these signs are detected, consider replacing the felt belt in a timely manner. This proactive approach can prevent more serious problems from occurring and ensure the stable operation of the equipment. - Optimal Tension Adjustment
Learn to correctly adjust the tension of the felt belt. Refer to the equipment’s manual for the recommended tension range. Use tension – measuring tools to ensure that the tension is within the appropriate limits. Regularly check and readjust the tension as the belt wears to maintain its proper operation. - Tool Maintenance and Optimization
Keep the cutting tools sharp and well – aligned. Regularly replace dull tools and ensure that they are correctly installed. This can reduce the uneven pressure on the felt belt and minimize the risk of fraying. Additionally, consider using tools with a design that reduces friction with the felt belt, such as those with special coatings or profiles. - Environmental Control
If possible, control the working environment. Install dehumidifiers in high – humidity areas to keep the moisture level in check. In areas with extreme temperatures, consider using temperature – control systems to maintain a suitable working environment for the felt belt. This can help extend the lifespan of the felt belt and reduce the occurrence of cracking and fraying.
Conclusion
Cracking and fraying of felt belts in vibration knife and cutting machine equipment are problems that can be effectively addressed. By understanding the causes and implementing the appropriate solutions, we can improve the performance and reliability of the equipment, reduce production disruptions, and ultimately enhance the overall efficiency of the manufacturing process. Remember, proper maintenance and attention to detail are key to ensuring the long – term health of your equipment’s felt belts.